10 passos para elaboração de um FMEA
Olá a todos, hoje vamos explorar um processo valioso para garantir a qualidade e a confiabilidade de produtos e processos. Estamos prestes a mergulhar nos 10 passos essenciais para a elaboração de uma Análise de Modo e Efeito de Falha, ou FMEA. Esta metodologia sistemática nos ajuda a identificar potenciais problemas e a tomar medidas preventivas para evitar falhas em produtos e processos. Vamos desvendar cada passo e compreender como aplicá-los de maneira eficaz para garantir a excelência em nossos empreendimentos.
Introdução
A Análise de Modo e Efeito de Falha (FMEA) é uma técnica robusta e estruturada amplamente utilizada em diversas indústrias para antecipar problemas e melhorar a qualidade. Ela é uma ferramenta valiosa que nos permite avaliar os riscos associados a falhas em produtos ou processos, ajudando a priorizar ações de prevenção e correção. Neste contexto, exploraremos os 10 passos cruciais para conduzir uma FMEA de forma eficaz. Cada passo desempenha um papel vital na identificação e mitigação de riscos, garantindo que nossos produtos e processos alcancem os mais altos padrões de qualidade e confiabilidade.
Todos os FMEAs de produto/design e de processo seguem esses dez passos:
- Revisar o processo/produto.
- Brainstorming de Modos de Falha Potenciais
- Listar os possíveis efeitos de cada modo de falha.
- Atribuir uma classificação de severidade para cada efeito.
- Atribuir uma classificação de ocorrência para cada modo de falha.
- Atribuir uma classificação de ocorrência para cada modo de falha.
- Calcular o número de prioridade de risco para cada efeito.
- Calcular o número de prioridade de risco para cada efeito.
- Tomar medidas para eliminar ou reduzir os modos de falha de alto risco.
- Calcular o RPN resultante à medida que os modos de falha são reduzidos ou eliminados.
Planilha de FMEA
A análise FMEA (Análise de Modo e Efeito de Falha) deve ser documentada utilizando uma planilha FMEA (conforme ilustrado na Figura abaixo). Este formulário captura todas as informações importantes sobre a FMEA e serve como uma excelente ferramenta de comunicação.
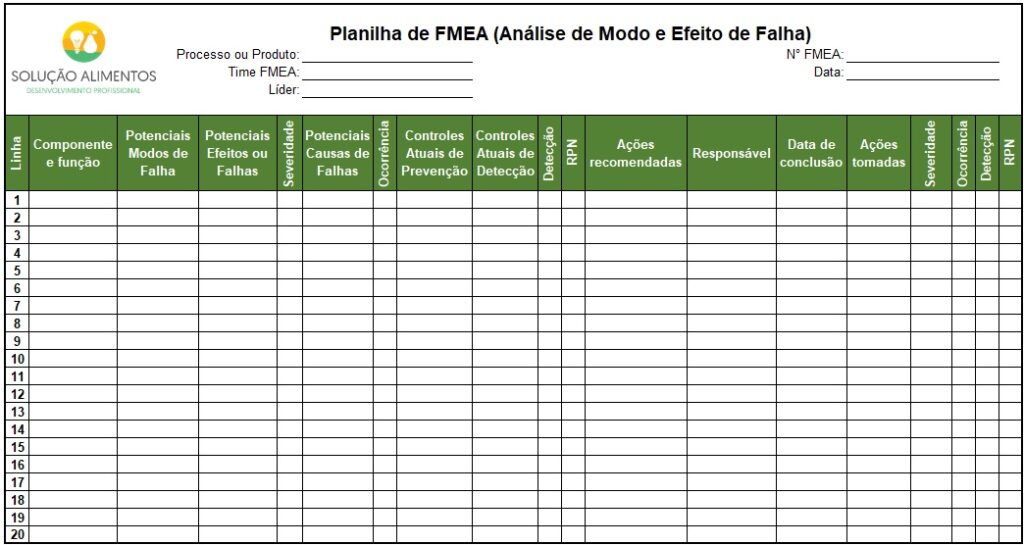
Passo 1: Revisar o Processo/Produto
A equipe deve revisar uma planta (ou desenho de engenharia) do produto se estiverem considerando uma FMEA de produto ou um fluxograma detalhado da operação se estiverem conduzindo uma FMEA de processo. Isso ajudará a garantir que todos na equipe de FMEA tenham a mesma compreensão do produto ou processo em que estão trabalhando.
Se uma planta ou fluxograma não estiverem disponíveis, a equipe precisará criar um antes de iniciar o processo de FMEA. Com a planta ou fluxograma em mãos, os membros da equipe devem se familiarizar com o produto ou processo. Para uma FMEA de produto, eles devem ver fisicamente o produto ou um protótipo dele. Para uma FMEA de processo, a equipe deve percorrer fisicamente o processo exatamente como ele ocorre. É útil ter um “especialista” no produto ou processo disponível para responder a qualquer pergunta que a equipe possa ter.
Passo 2: Brainstorming de Modos de Falha Potenciais
Assim que todos na equipe compreenderem o processo (ou produto), os membros da equipe podem começar a pensar nos modos de falha potenciais que poderiam afetar o processo de fabricação ou a qualidade do produto. Uma sessão de brainstorming permitirá que todas essas ideias sejam apresentadas. Os membros da equipe devem chegar à reunião de brainstorming com uma lista de suas ideias. Além das ideias que os membros trazem para a reunião, outras serão geradas como resultado da sinergia do processo em grupo.
Devido à complexidade da maioria dos produtos fabricados e dos processos de fabricação, é melhor realizar uma série de sessões de brainstorming, cada uma focada em um elemento diferente (ou seja, pessoas, métodos, equipamentos, materiais e o ambiente) do produto ou processo. Focar nos elementos um de cada vez resultará em uma lista mais completa de modos de falha potenciais.
Não é incomum gerar dezenas de ideias a partir do processo de brainstorming. Na verdade, esse é o objetivo! Uma vez que o brainstorming esteja completo, as ideias devem ser organizadas agrupando-as em categorias semelhantes. Sua equipe deve decidir as melhores categorias para agrupar, pois existem muitas maneiras diferentes de agrupar modos de falha. Você pode agrupá-los pelo tipo de falha (por exemplo, elétrica, mecânica, criada pelo usuário), onde no produto ou processo a falha ocorre, ou a gravidade (pelo menos o melhor palpite da equipe neste ponto) da falha. Agrupar as falhas tornará o processo de FMEA mais fácil de ser trabalhado. Sem a etapa de agrupamento, a equipe pode gastar muita energia pulando de um aspecto do produto para outro completamente diferente e depois voltando novamente. Uma maneira fácil de trabalhar o processo de agrupamento é colocar todos os modos de falha em notas autoadesivas e colocá-los em uma parede para que sejam fáceis de ver e mover enquanto estão sendo agrupados.
O agrupamento também dá à equipe a chance de considerar se alguns modos de falha devem ser combinados, porque são iguais ou muito semelhantes entre si. Quando os modos de falha forem agrupados e combinados, se apropriado, eles devem ser transferidos para a planilha de FMEA. Geralmente, existem vários modos de falha para cada componente.
Passo 3: Listar os Efeitos Potenciais para Cada Modo de Falha
Com os modos de falha listados na planilha de FMEA, a equipe de FMEA revisa cada modo de falha e identifica os efeitos potenciais da falha (caso ela ocorra). Para alguns dos modos de falha, pode haver apenas um efeito, enquanto para outros pode haver vários efeitos.
Este passo deve ser minucioso, pois essa informação será usada para atribuir classificações de risco para cada uma das falhas. É útil pensar neste passo como um processo de “se-então”: Se a falha ocorrer, então quais são as consequências?
Passos 4 a 6: Atribuir Classificações de Severidade, Ocorrência e Detecção
Cada uma dessas três classificações é baseada em uma escala de 10 pontos, sendo 1 a classificação mais baixa e 10 a mais alta.
É importante estabelecer descrições claras e concisas para os pontos em cada uma das escalas, de modo que todos os membros da equipe tenham a mesma compreensão das classificações. As escalas devem ser estabelecidas antes que a equipe comece o processo de classificação. Quanto mais descritiva a equipe for ao definir a escala de classificação, mais fácil será chegar a um consenso durante o processo de classificação.
A importância de ter um conjunto comum de escalas de classificação tanto para processo quando para design em toda a organização é que as classificações e os números de prioridade de risco resultantes entre as FMEAs têm uma relação entre si. Isso permite que a organização compare RPNs entre FMEAs para priorizar ainda mais as atividades de melhoria.
Mesmo que o sistema de classificação seja claro e conciso, ainda pode haver discordância sobre a classificação de um item específico. Nesses casos, o grupo precisa chegar a um consenso.
Passo 4: Atribuir uma Classificação de Severidade para Cada Efeito
A classificação de severidade é uma estimativa de quão graves seriam os efeitos se uma determinada falha ocorresse. Em alguns casos, é claro, devido à experiência passada, o quão grave o problema seria. Em outros casos, é necessário estimar a gravidade com base no conhecimento e na experiência dos membros da equipe.
É importante observar que, como cada falha pode ter vários efeitos diferentes, e cada efeito pode ter um nível diferente de severidade, é o efeito, não a falha, que é avaliado. Portanto, cada efeito deve receber sua própria classificação de severidade, mesmo que haja vários efeitos para um único modo de falha.
Passo 5: Atribuir uma Classificação de Ocorrência para Cada Modo de Falha
O melhor método para determinar a classificação de ocorrência é usar dados reais do processo. Isso pode estar na forma de registros de falhas ou até mesmo dados de capacidade do processo. Quando dados reais de falhas não estão disponíveis, a equipe deve estimar com que frequência um modo de falha pode ocorrer. A equipe pode fazer uma estimativa melhor de quão provável é que um modo de falha ocorra e com que frequência, conhecendo a causa potencial da falha. Uma vez que as causas potenciais tenham sido identificadas para todos os modos de falha, uma classificação de ocorrência pode ser atribuída, mesmo que os dados de falha não existam.
Passo 6: Atribuir uma Classificação de Detecção para Cada Modo de Falha e/ou Efeito
A classificação de detecção analisa quão provável é que detectemos uma falha ou o efeito de uma falha. Começamos este passo identificando os controles atuais que podem detectar uma falha ou o efeito de uma falha. Se não houver controles atuais, a probabilidade de detecção será baixa, e o item receberia uma classificação alta, como 9 ou 10. Primeiro, os controles atuais devem ser listados para todos os modos de falha ou os efeitos das falhas, e então as classificações de detecção são atribuídas.
Passo 7: Calcular o Número de Prioridade de Risco para Cada Modo de Falha
O número de prioridade de risco (RPN) é simplesmente calculado multiplicando a classificação de severidade pela classificação de ocorrência pela classificação de detecção para cada item.
Número de prioridade de risco= Severidade x Ocorrência x Detecção
O número total de prioridade de risco deve ser calculado somando todos os números de prioridade de risco. Esse número, por si só, não tem significado, pois cada FMEA possui um número diferente de modos de falha e efeitos. No entanto, ele pode servir como um indicador para comparar o RPN total revisado uma vez que as ações recomendadas tenham sido implementadas.
Passo 8: Priorizar os Modos de Falha para Ação
Os modos de falha podem agora ser priorizados classificando-os em ordem, do número de prioridade de risco mais alto para o mais baixo. Assim como em outros processos de melhoria da qualidade, pode se aplicada a regra 80/20 aos RPNs. No caso do RPN, uma tradução literal significaria que 80 por cento do RPN total para a FMEA vem de apenas 20 por cento das falhas e efeitos potenciais. Um diagrama de Pareto é útil para visualizar as diferenças entre as classificações dos modos de falha e efeitos.
A partir desse momento, a equipe deve decidir em quais itens trabalhar. Geralmente, ajuda definir um RPN de corte, onde quaisquer modos de falha com um RPN acima desse ponto são tratados. Aqueles abaixo do limite são deixados de lado por enquanto. Por exemplo, uma organização pode decidir que qualquer RPN acima de 200 cria um risco inaceitável. Essa decisão define o RPN de corte em 200.
Passo 9: Tomar Ações para Eliminar ou Reduzir os Modos de Falha de Alto Risco
Usando um processo de solução de problemas organizado, identifique e implemente ações para eliminar ou reduzir os modos de falha de alto risco. Idealmente, os modos de falha devem ser eliminados completamente. Quando um modo de falha é eliminado completamente, o novo número de prioridade de risco se aproxima de zero porque a classificação de ocorrência se torna um.
Embora a eliminação completa dos modos de falha seja o ideal, pode não ser alcançável em todos os casos. Quando isso acontece, ajuda voltar às classificações de severidade, ocorrência e detecção que a equipe atribuiu a cada item. Pense em maneiras de reduzir as classificações em uma, duas ou todas as três escalas.
Muitas vezes, a abordagem mais fácil para fazer uma melhoria no processo ou produto é aumentar a detecção da falha, diminuindo assim a classificação de detecção. Por exemplo, uma cafeteira pode ter um sinal sonoro a cada dez minutos para lembrar que está ligada e que você precisa desligá-la antes de sair de casa, ou um fabricante de computadores pode incluir um software que notifica o usuário que há pouco espaço em disco.
No entanto, essas são abordagens paliativas que muitas vezes são caras e não melhoram efetivamente a qualidade do produto. Aumentar a detecção de falhas simplesmente tornará mais fácil detectar as falhas quando elas ocorrerem.
Reduzir a severidade é importante, especialmente em situações que podem levar a lesões. Por exemplo, uma empresa que fabrica equipamentos pode limitar a velocidade de uma máquina, reduzindo a gravidade de uma possível lesão pessoal. No entanto, a oportunidade mais importante para melhoria está em reduzir a probabilidade de ocorrência da falha. Afinal, se é altamente improvável que ocorra uma falha, há menos necessidade de medidas de detecção.
Passo 10: Calcular o RPN Resultante à Medida que os Modos de Falha São Reduzidos
Depois que ações foram tomadas para melhorar o produto ou processo, novas classificações de severidade, ocorrência e detecção devem ser determinadas, e um RPN resultante deve ser calculado.
Para os modos de falha em que foram tomadas medidas, deve haver uma redução significativa no RPN. Caso contrário, isso significa que as ações não reduziram a severidade, probabilidade de ocorrência ou capacidade de detecção.
Os RPNs resultantes podem ser organizados em um diagrama de Pareto e comparados com os RPNs originais. Além disso, os RPNs totais do produto ou processo antes e depois podem ser comparados e contrastados. Você deve esperar uma redução de pelo menos 50 por cento no RPN total após uma FMEA.
Não existe um RPN-alvo para FMEAs. Cabe à equipe de FMEA e à empresa decidir até onde a equipe deve ir com as melhorias. Sempre haverá a possibilidade de ocorrerem modos de falha. A pergunta que a empresa deve fazer é quanto risco relativo a equipe está disposta a assumir. A resposta dependerá da indústria e da gravidade da falha. Por exemplo, na indústria nuclear, há pouco espaço para erros; eles não podem correr o risco de ocorrer um desastre. Em outras indústrias, pode ser aceitável assumir riscos mais altos. Se a equipe estiver satisfeita com o RPN resultante, ela deve apresentar os resultados da FMEA à administração, que determinará se devem ser realizados trabalhos adicionais para reduzir ainda mais os RPNs.